
Ball mill- what is the % of filling by balls and % of ...
Ball mill- what is the % of filling by balls and % of filling by materials ? ball mill size dia=2 meter, length 8 m, inner dia= 1.888 m , material to be grinded= illuminate, ball size= 20,30,40 mm ...

Ball Mill Filling Calculation - munstersbelettering.nl
calculation in filling ratio for ball mill. calculation in filling ratio for ball mill. Cement Ball Mill Sizing Explanation The Cement Grinding Office Efficiency correction factors are applied with the Bond equation This method only gives a rough and initial idea for sizing a cement ball mill difference is higher, ...
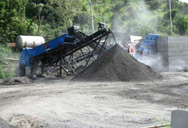
calculation in filling ratio for ball mill
iron ore ball mill grinding media filling ratio calculation. Ball Mill for Sale Grinding MachineJXSC Mining Ball mill is the key equipment for grinding materials. those grinding mills are widely used in the mining process and it has a wide range of usage in grinding mineral or material into fine powder such as …

calculation of ball filling ratio in grinding mill
About volume filling of grinding media in cement ball mill iron ore ball mill grinding media filling ratio . >>Chat Online; Aside from common ball mills there is a second type of ball mill . More. Ball Mill Parameter Selection Calculation - Power .

Ball Mill - an overview | ScienceDirect Topics
Ball mills tumble iron or steel balls with the ore. The balls are initially 5–10 cm diameter but gradually wear away as grinding of the ore proceeds. The feed to ball mills (dry basis) is typically 75 vol.-% ore and 25% steel. The ball mill is operated in closed circuit with a particle-size measurement device and size-control cyclones.

How to Size a Ball Mill -Design Calculator & Formula
A) Total Apparent Volumetric Charge Filling – including balls and excess slurry on top of the ball charge, plus the interstitial voids in between the balls – expressed as a percentage of the net internal mill volume (inside liners). B) Overflow Discharge Mills operating at low ball fillings – slurry may accumulate on top of the ball charge; causing, the Total Charge Filling Level to ...

Ball Mills - an overview | ScienceDirect Topics
The degree of filling the mill with balls also influences productivity of the mill and milling efficiency. With excessive filling, the rising balls collide with falling ones. Generally, filling the mill by balls must not exceed 30–35% of its volume. Productivity of ball mills depends on drum diameter and the relation of drum diameter and length.

A Method to Determine the Ball Filling, in Miduk Copper ...
to ball filling variation in the mill. The results obtained from this work show, the ball filling percentage variation is between 1.2– 3.7% which is lower than mill ball filling percentage, according to the designed conditions (15%). In addition, acquired load samplings result for mill ball filling was 1.3%.

Best way to determine the ball-to-powder ratio in …
As for as ball to powder ratio is concerned, if the purpose is mixing you should go for 5-10 ration of ball with powder. In case if you want to reduce the size or ally the powder then select high ...

Optimization of mill performance by using
previously, at a mill stop, the measurement of ball charge filling degree could be undertaken and will provide the static media charge angle (βstatic = 143°). An online measurement of the similar angle (βdynamic), when the mill is running, provides information about the dynamics of the charge. The ratio between the dynamic and the static ...

air to material ratio in ball mill separator
Ore Dressing High Ball Mill Ratio Ball Mill Machinery. Ore dressing wet process ball millrolvaplast.Typically, this product is found in ore beneficiation process and aerated concrete plant.Ore dressing ball millcompared with traditional ball mill, the ore dressing ball mill fan saves power from 18 to 25, lubrication of 70 and cooling water of 90, and comprehensively save energy above 20.

TECHNICAL NOTES 8 GRINDING R. P. King
Figure 8.5 Effect of mill filling on power draft for ball mills. The data is taken from Rexnord Process Machinery Reference Manual, Rexnord Process Machinery Division, Milwaukee, 1976 The effect of varying mill speed on the power drawn by the mill is shown graphically in Figure 8.4 The speed of rotation of the mill influences the power draft ...

Ball mill - Wikipedia
A ball mill is a type of grinder used to grind, blend and sometimes for mixing of materials for use in mineral dressing processes, paints, pyrotechnics, ceramics, and selective laser sintering.It works on the principle of impact and attrition: size reduction is done by impact as the balls drop from near the top of the shell. A ball mill consists of a hollow cylindrical

calculation of filling volume in ball mill
Ball mills have large applicability in the mining industry. At the same ... media and intermediate degree of both mil filling and percentage of solids. ..... Figure 3-2: Comminution energy efficiency calculated using ratio between operating ..... Mill filling is the percentage of the mill volume occupied by the grinding media and the. Get Price

Calculate Ball Mill Grinding Capacity
The sizing of ball mills and ball milling circuits from laboratory grinding tests is largely a question of applying empirical equations or factors based on accumulated experience. Different manufacturers use different methods, and it is difficult to check the validity of the sizing estimates when estimates from different sources are widely divergent. It is especially difficult to teach mill ...

ball mill and ball mill motor ratio - …
ball mill length and diameter ratio - ball mill, length and diameter ratio. Ball Mill Instruction Manual (PDF) BICO Inc. The F.C. Bond Ball Mill is a small universal oratory mill used in calculating the grindability of ranging in size from 3/4 inch to 1-1l2 inch in diameter, and weighing approKimately 20,125 grams. 700 CC.. tho reduciion ratio Rr is J/p Accordios to KICK, tbc shape, thc @ck ...

Cement mill notebook - LinkedIn SlideShare
The difference between ball mill and tube mill is the ratio of the tube length to the tube diameter. Tube mills have a ratio of length to diameter of [3-6 : 1], for ball mill this relation is ... Example: Two compartment cement mill Diameter = 4.05 m Length = 12 m Filling degree = 196 tons at 30% filling degree Mill speed = 16.27 rpm C = 0.223 ...

THE OPTIMAL BALL DIAMETER IN A MILL
The ball impact energy on stone is proportional to the ball diameter to the third power: 3 E K 1 d b. (3) The coefficient of proportionality K 1 directly depends on the mill diameter, ball mill loading, milling rate and the type of grinding (wet/dry). None of the characteristics of the material being ground have any influence on K 1.

Mill (grinding) - Wikipedia
A VSI mill throws rock or ore particles against a wear plate by slinging them from a spinning center that rotates on a vertical shaft. This type of mill uses the same principle as a VSI crusher.. Tower mill. Tower mills, often called vertical mills, stirred mills or regrind mills, are a more efficient means of grinding material at smaller particle sizes, and can be used after ball mills in a ...