
Direct Reduction Process - an overview | ScienceDirect Topics
The basis of the direct reduction process is that solid sponge iron is produced by removing oxygen from the ore in a shaft furnace, rotary kiln furnace or fluidised bed. Sponge iron can be produced in the form of Direct Reduced Iron (DRI), Hot Briquetted Iron (HBI) and Cold Briquetted Iron (CBI); also Low Reduced Iron (LRI), which is pre-reduced iron ore with a reduction and metallisation degree lower …

Direct Reduction Of Iron Ore From Tunnel Kiln Process ...
Sponge Iron Production Using Tunnel Kiln Report Iron Ore Asri Keramik heavily promoted the use of Tunnel Kiln to produce sponge iron on following basis a Tunnel Kiln is the most effective method for direct reduction process as the firing temperature is controlled and Slrn Process Outotec

tunnel kiln process of i ron ore reduction 」
The direct reduction process uses pelletized iron ore or natural "lump" ore. One exception is the fluidized bed process which requires sized iron ore particles. Inquire Now; Tunnel Kiln Process Sponge Iron Technology Consulting Gold

Direct Reduction Of Iron Ore From Tunnel Kiln Process
Reduction Reaction In Tunnel Kiln Process For Iron Ores. Patent wo2013011521a1 a method for direct . title a method for direct reduction of oxidized chromite ore fines composite agglomerates in a tunnel kiln using carbonaceous reductant for production of reduced. read more direct reduced iron and its production processes. More Details

Tunnel Kiln Process Of Iron Ore Reduction
tunnel kiln process of iron ore reduction. tunnel kiln process of iron ore reduction_cha irom ore pelletion kiln dese process psco.red ruby diamond prices tamilnadu. Ruby Wikipedia, the free encyclopedia. are also an important factor determg the price.

Direct Reduced Iron and its Production Processes – IspatGuru
Mar 16, 2013 · Fig 2 Principle of direct reduction process. Gas based process. In the gas based reduction processes, a vertical shaft kiln is used in which iron ore is fed into the top of the kiln and finished sponge iron is drawn off from the bottom after cooling it so as to prevent its re-oxidation.

calculation on reduction for direct reduced iron in tunnel ...
This process produces iron directly from fine iron ore concentrate by a gas-solid suspension reduction, utilizing hydrogen as the main reducing agent for high ... calculations have shown that the process would drastically reduce energy ..... annually since the total retention time in …
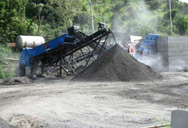
Coal based Direct Reduction Rotary Kiln Process – IspatGuru
The metallic iron in this process is produced by the reduction of iron oxide below the fusion temperature of iron ore (1535 deg C) by utilizing carbonaceous material present in the non-coking coal. As the iron ore is in direct contact with the reducing agent throughout the reduction process, it is often termed as direct reduced iron (DRI).

tunnel kiln iron ore technology, - vedes-charter.be
The Use Of Tunnel Kiln For Iron Ore Reduction. tunnel kiln iron ore technology alsdseu direct reduced iron tunnel kiln direct reduction of iron ore from tunnel kiln process 390 Views The is the professional mining equipments manufacturer in the world located in China India iron ore pellets manufacturing process by tunnel kiln Ore Car For Sale ...

tunnel kiln iron ore - witchcraftpsychic.co.za
Direct reduction of iron ore by one or more processes un- der study by steel .... ore in a vertical shaft furnace, a rotary or tunnel kiln, or other types of hearth or. Get Price Tunnel Kiln - Manufacturers, Suppliers & Exporters - IndiaMART

(PDF) i) Direct Reduced Iron: Production
During the last four decades, a new route of ironmaking has rapidly developed for direct reduction (DR) of iron ore to metallic iron by using noncoking coal/natural gas. This product is known as...

SPONGE IRON PRODUCTION FROM ORE -COAL COMPOSITE …
In the year 1908 use of tunnel kiln started for iron oxide reduction. This process was invented by E.Sieurin as Hoganas process [3]. In 1954, more kilns came in operation in SWEDEN and USA. Presently it is more popular in China for sponge iron production from beneficiated iron ore fines cakes. In this process, the material passes through

Direct reduced iron - Wikipedia
The direct reduction process uses pelletized iron ore or natural "lump" ore. One exception is the fluidized bed process which requires sized iron ore particles. The direct reduction process can use natural gas contaminated with inert gases, avoiding the need to remove these gases for other use.

direct reduction of iron ore from tunnel kiln process
Direct reduction of iron ore from tunnel kiln processron ore reduction in tunnel kiln solution for ore miningirect reduction of iron ore from tunnel kiln process process the caiman is the professional mining equipments manufacturer in the world loed in china india along with other asian marketplaces to develop and develop now we More DRI Tunnel Kiln Industrial Furnaces Ovens Case The

Direct Reduced Iron Technology In Tunnel Kiln
Direct reduced iron technology in tunnel kiln direct reduction of iron ore from tunnel kiln process dri tunnel kiln direct reduction.By using tunnel kiln to produce dri is that mix the iron ore concentrate, pulverized coal and limestone powder with certain proportion and feed into material drum for being reduction, and then put these drums on the kiln car and pushed it into the tunnel kiln.

Direct-Reduced Iron - an overview | ScienceDirect Topics
The RHF process was originally developed as an alternative to gas-based direct reduction, making DRI from iron ore and coal. The process started from the patent of D. Beggs applied by Midland-Ross Corporation in 1965 [144]. This process was known as Heat Fast [145]. Tests to reduce fine iron ore were carried out using a pilot plant (2 tons/h) in Minnesota, USA in 1965.

REITEC TUNNEL KILN DIRECT REDUCTION BRIQUETTE ...
REITEC TUNNEL KILN DIR PROCESS. 1-Iron ore powder.Feeding Iron ore powder which contains 8-10%. moisture, into drying machine for drying..Heat of the drying machine comes the surplus. heat of tunnel kiln cooling section. TFe 60-64% iron ore fine powder (Magnetite or Hematite) In case TFe is less that 60% we can increase Fe by

Sponge Iron Production Process - Arij Trading
This process is one of the oldest direct reduction methods and the idea of its structure is based on a horizontal cement kiln. In this method, heat coal (as a reducing agent) is mixed with iron ore and sponge iron is produced in a horizontal furnace.

DRI production | International Iron Metallics Association
coal based rotary kiln furnaces (mainly in India) - accounting for 17.5% of 2016 production. Generic illustrations of the types of process are shown in the graphics below. Overview of direct reduction process types. Direct reduction furnace types. Direct reduction processes for iron. Illustrations of the principal processes are shown below.